降低液力耦合器滑差率,有2种方案可供选择:
1)对给水泵叶轮进行车削,降低给水泵在原有工作转速下的压头和流量。当需要达到原有的压头和流量情况下,就必须提高给水泵(热泵)的工作转速,从而达到降低液力耦合器滑差率的目的。
2)对液力耦合器进行改造,减小液力耦合器增速齿轮的传动比,这样就可以降低泵轮转速,使液力耦合器输出端的转速与给水泵满负荷工况下的工作转速接近,从而达到降低液力耦合器滑差率的目的。
对比以上2种方案,第1种方案投资小,风险较低,但计算比较困难。第2种方案投资较大,风险较高,但能够计算出改造后给水泵的运行参数。经过综合比较,我们终选择投资较小,风险较低的第1种方案,即对给水泵叶轮进行车削。
2改造效果理论测算
采取几种不同的方法对改造后的给水泵节能效果进行理论测算。
2.1根据液力耦合器效率进行计算
1)车削叶轮前液力耦合器效率:
2)车削叶轮后液力耦合器效率:
3)车削叶轮前后功率损失差值
2.2根据液力耦合器功率损失进行计算
2.3根据能量平衡的方法进行计算
根据液力耦合器的理论,其在工作中的功率损失终全部转变为热量,这些热量一部分通过液力耦合器的零部件,壳体向周围散热,绝大部分加热了工作液体,使工作液体温度升高,因此通过测定工作油冷油器和润滑油冷油器的温升,就可以知道液力耦合器的功率损失。因为测定油的流量比较困难,通过测量冷却水的流量来计算其换热量的大小,也可以间接知道液力耦合器的功率损失。用机组在220MW负荷下的工况和在190MW负荷下的工况作对比.
前2种方法计算出的结果偏小,主要有以下原因:
1)在机组带同样的220MW负荷工况下与机组分别带220MW,190MW工况时,由于后者液力耦合器的输入功率下降(220MW大约为4250kW,而190MW时大约为3900kW),在液力耦合器效率同样下降的情况下,其功率损失值也小些,如果以液力耦合器效率下降4计算,其功率损失值偏小14kW.
2)以上计算没有考虑通过液力耦合器壳体等部位向外的散热量。
因此,如果通过叶轮车削,给水泵转速由4650 r/min升至5000r/min,滑差率减少6.6,功率损失应该在200kW左右。
实际上,好的方法是通过计算在不同的滑差率下液力耦合器的效率,然后按照其输入功率计算功率损耗差值。但这种方法需要测定前置泵,给水泵,电机的轴承等部位所产生的摩擦损失,基于现实条件,很难做到,因此采取以上的计算方法来估算还是比较可行的。
比较以上3种计算方法可知,如果能够知道工作油流量和润滑油流量,采用能量平衡法比较合适。
几种方法虽然计算上都有误差,但通过估算可以预测出柳电公司给水泵车削叶轮后液力耦合器的功率损失至少可减少约200kW,节能效果显着,经济效益非常可观。
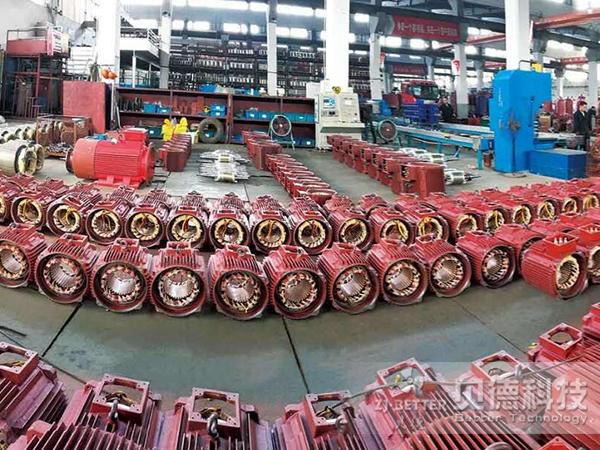